the quality control of welded structural steel pipe
Due to proper wall thickness, good material, processing technology and stability, structural steel has become the first choice for large domestic and foreign oil and natural gas line pipe projects. In the large straight seam welded steel pipe joint structure, weld and heat affected zone is the easiest place to produce a variety of defects, weld undercut, pores, slag, lack of fusion and lack of penetration. Weld cracking is the main form of welding defects and easy to cause structural steel quality accidents origin.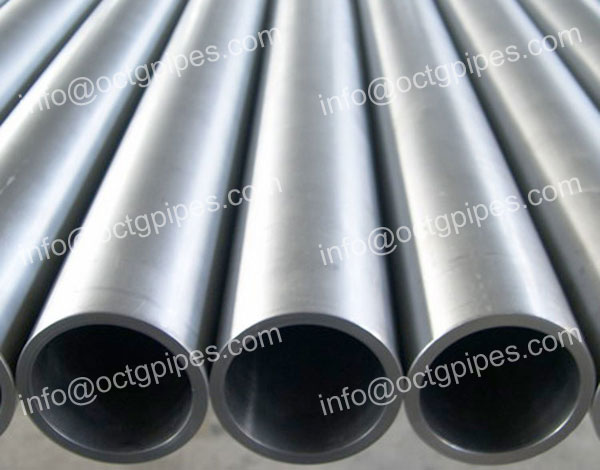
The Measures for Structural Steel Quality Control As Following:
Welding quality control:
► Make high quality raw materials, then pass inspection before being officially entered the construction site and resolutely put an end to the use of standard steel.
► The management of welding materials. Check if the welding materials are qualified; whether the storage and baking system is achieved; whether the surface of welding material is clean without rust; whether the electrode coating intact is completed without mould.
► The clean management of welding area. The clean quality inspection for welding zone without water, oil, rust and dirt oxide film. It is an important factor for the cleaning quality to prevent external welded defects.
► Select proper welding method. The method should be implemented the test welding and welding principles.
Quality control in the welding process
◆ According to welding process specifications, the wire and flux review is correct to prevent misuse wire and flux caused by welding quality accident.
◆ The welding environment supervision. Take appropriate steps after welding. When welding environment is not good (temperature below 0℃, relative humidity greater than 90%) should be.
◆ Before the expected first test welding, the groove dimensions including space, blunt space, blunt edge, the angle and the wrong mouth need to meet the process requirements.
◆ Make sure the choice of welding current, welding voltage, welding speed and other parameters are correct during the inside and outside the submerged arc welding process.
◆ Let the staff make full use of steel tube and plate length inside and outside during the submerged welding process and straight seam strengthen the efficiency of the welding arc for the inner and outer plates. This will help to improve the quality of welding the pipe ends.
◆ Let the welder check the welding slag is whether clean first; if the joint has been completely processed; whether the groove of the oil, rust slag water paint and other contaminants is cleared.
Get In Touch